How to ensure H2S safety on offshore rigs
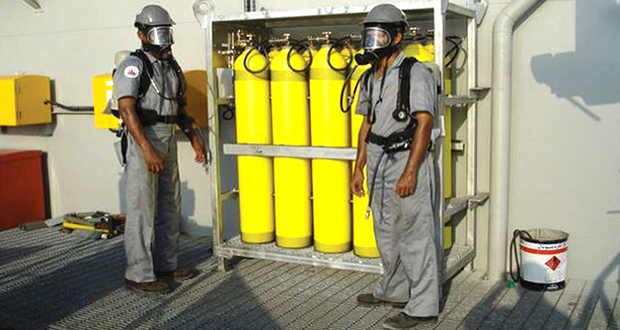
By Angelo Pinheiro, Marathon Oil
Hydrogen sulfide (H2S) is a toxic, flammable and corrosive gas often encountered during hydrocarbon exploration and production. It is a byproduct of the decay of protein-containing substances, forming by bacterial reduction of sulfates in sedimentary rocks. Hydrogen sulfide may also be anticipated in previously uncontaminated reservoirs into which sulfate-reducing bacteria were introduced through workover and completion fluids containing organic polymers, including starch, methyl cellulose and polysaccharide base additives. It is important to recognize the potentially dangerous H2S exposure limits.
SIGNIFICANCE OF PROBLEM
H2S is extremely toxic to humans at minute concentrations. At higher concentrations it is flammable, as well as corrosive to metals. A surface breakout of this gas, if not responded to and controlled immediately, can result in injuries and/or fatalities, fire and explosion.
If an H2S event were to occur during adverse weather, then personnel evacuation from the affected rig, plus vessels and installations downwind, could be severely compromised. Drilling and well control equipment that are not designed for H2S use could suffer a loss of structural integrity following exposure, which could impede their function and operation during an emergency.
A blowout involving H2S has the potential to disrupt maritime transportation, fishing, and manned oil and gas infrastructure downstream of the source. The loss of life and disruption to business continuity could result in substantial financial and legal liability, compensation claims, fines and potential prosecution.
PROPERTIES, EFFECTS, INCIDENCE
In the presence of moisture, H2S forms sulfurous and sulfuric acids, which are corrosive to metals. Corrosivity is enhanced in the presence of carbon dioxide and produced water low in oxygen content. The effects of H2S corrosion include hydrogen embrittlement, corrosion, and cracking of drillstring components, drilling fluid processing equipment, and drilling safety equipment, such as blowout preventers. Tensile stress on the suspended drillstring exacerbates the effects of corrosion and causes “sulfide stress cracking.”
Physiological Effects of H2S Exposure
The primary route of exposure is by inhalation. In concentrations less than or around 50 parts per million (ppm), H2S acts as a mucous membrane and respiratory tract irritant. H2S exposure symptoms include:
- Coughing
- Shortness of breath
- Eye and throat irritation
At concentrations of approximately 100 ppm, H2S paralyzes the olfactory nerve and the sense of smell. It is rapidly absorbed by the lungs and transferred to the blood circulation, where it inhibits the cytochrome oxidase enzyme system, which regulates the uptake of oxygen at the cellular level.
As the nervous system and cardiac tissues are particularly vulnerable to oxygen deprivation, symptoms such as headaches, disorientation, cyanosis, pulmonary edema, pulmonary hemorrhage and cardiac arrhythmia may follow. At 700 ppm to 1000 ppm, H2S acts as a chemical asphyxiant and produces rapid loss of consciousness, followed by death if the victim is not immediately rescued and resuscitated.
Occupational Exposure Levels
H2S has an immediately dangerous to life and health (IDLH) concentration of 100 ppm. For an airborne contaminant, IDLH is defined as the level of the contaminant likely to cause death or immediate or delayed permanent adverse health effects in the event of failure of the respiratory protection equipment. Most work areas on an offshore drilling rig are considered IDLH, as H2S is commonly encountered over 100 ppm and can stack up (increase in concentration) in low-lying areas or still wind conditions.
H2S has a permissible exposure level – ceiling concentration (PEL-C) of 20 ppm with an acceptable maximum peak above the acceptable ceiling concentration of 50 ppm once during an eight-hour work shift and which does not exceed 10 minutes (29 CFR 1910.1000). PELs are stipulated by OSHA and are legally binding.
Recommended Limits of H2S Exposure
- 10 ppm for an 8-hour workday, 40-hour work week is the threshold limit value (TLV)
- 15 ppm is the short-term exposure limit per ACGIH, 2009
TLVs and short-term exposure limits (STELs) are recommendations of the American Conference of Government Industrial Hygienists (ACGIH) and are voluntary standards. As offshore work schedules involve 12-hour shifts seven days a week, up to 4 weeks at a time, the TLV should be adjusted as the period of elimination is decreased. That may be done using several methods, one of which is the Brief & Scala method.
The Brief & Scala method for threshold limit value adjustments:
Adjusted Daily TLV = [TLV x Daily Reduction Factor]
= [TLV x (8/hd) x {(24-hd)/16}] = 5 ppm
Adjusted Weekly TLV = (TLV x Weekly Reduction Factor)
= [TLV x (40/hw) x {(168-hw)/128}] = 3.125 ppm
It is common practice on offshore drilling rigs to set the low and high alarms of H2S area monitoring systems at the unadjusted TLV and STEL level of 10 ppm and 15 ppm.
Where to anticipate H2S exposure
H2S should be anticipated in all areas of the rig where drilling fluid & associated equipment is present:
- Rig floor
- Substructure
- Shale shakers
- Mud cleaners
- Mud pit room
- Mud pump room
- Well test equipment
Being heavier than air, H2S will settle in low-lying and poorly ventilated areas and will dissolve in oil and water present in those areas.
When to anticipate H2S exposure
- When breaking out, i.e., when the “run in hole” of drill pipe has been completed and bottom fluids are displaced to surface
- When drill pipe is pulled out of the well too quickly, resulting in formation fluid entering the wellbore, or “swabbing”
- When retrieving core or fluid samples
- When flowing well testing
During well test operations involving flaring of formation fluids, H2S and sulfur dioxide should be anticipated around the rig and on the sea surface. Figure 1 illustrates a drilling mud system, Figure 2, a self-elevating drilling platform, and Figures 3-7, examples of rig areas and equipment where H2S may be encountered.
H2S RESPIRATORY PROTECTION PROGRAM
A written respiratory protection program and H2S contingency plan that are developed in the planning phase for the well will ensure the safety of all rig personnel. Safety planning should focus on prevention and accord priority to engineering controls, including:
- Mud weight control to ensure that hydrostatic pressure exerted by the mud column overbalances the formation pressure and prevents influx of gas into the mud column
- Continuous monitoring of drilling returns (mud and cuttings) for H2S
- Addition of H2S scavengers (zinc carbonate and ironite sponge) in drilling and completion fluid formulations
- Negative pressure ventilation and air locks in mud-processing rooms
- Local exhaust ventilation over the shale shakers
- Positive pressure ventilation of living quarters, with H2S monitoring at the air intake linked to HVAC shutdown
- Area monitoring system for H2S with strategically located sensors
- Supplied breathing air system in work areas and at muster/evacuation stations
- Corrosion rings to indicate drill pipe corrosion (they are subject simultaneously to corrosion and tensile and torsional stresses) and specifying NACE (North American Corrosion Engineers) standards for well control equipment and tubulars
- Arrangements for emergency flaring when the well cannot be shut
- Using dynamically positioned semisubmersible rigs (in preference to self-elevating or anchored semisubmersible rigs), which can be oriented to the wind direction without disrupting rig operations, such that gases are blown away from living and work areas.

A respiratory protection program complying with 29 CFR 1910.134(c) would include the following steps:
- Respirator selection.
- Fit testing for tight-fitting respirators.
- Medical evaluation.
- Procedures for reasonable foreseeable emergencies.
- Maintenance arrangements and procedures.
- Procedures for supplied air respirators (SAR).
- Training on use of respirators for routine and emergency situations
- Training in the donning, doffing, care and maintenance of the respirator selected.
- Procedures for evaluating effectiveness of the respiratory protection program.
The implementation of this standard are described below from an offshore drilling perspective.
Choosing a Respirator
Respiratory protective equipment for H2S is selected following an assessment of the hazard and exposure. The hazard assessment takes into consideration factors such as:
- Anticipated concentration
- Environmental/weather conditions, including seasonal wind directions, rig layout, the placement of temporary equipment onboard for the well test, personnel exposure patterns in terms of work activities, & duration of those activities
- Detection & monitoring arrangements
- Existing & required respiratory protection equipment
- NIOSH & DOT certification requirements for breathing apparatus and compressed air cylinders
- Engineering & administrative control measures that will be implemented
Personnel should be involved in respirator selection, and concerns such as comfort, fit and adaptability for use with other personal protective equipment should be considered. The assigned protection factor (APF) should be carefully reviewed in order to determine the maximum use concentration. The APF of a tight-fitting airline respirator is 1,000, which might be a limiting factor if the H2S concentration exceeds 10,000 ppm. An airline respiratory system is usually provided on offshore rigs to permit continuous work while masked up.
Important considerations in selecting/designing such a system include multistage compressors (to reduce charging time during an emergency), reserve air capacity, number and placement of low-pressure air manifolds, air pressure and flow requirements, capacity/size of the auxiliary air cylinder to permit escape, air quality requirements (CGA specification Grade D), low-pressure alarms, ability to communicate while masked up (i.e., speech diaphragm), etc.

Medical Evaluation
Employees required to use respirators must undergo a medical examination by a physician or licensed health care provider (PLHCP) in accordance with 29 CFR 1910.134(e)(2)(ii). A follow-up medical exam may be needed if a positive response was made in the health questionnaire or if deemed necessary by the PLHCP. The PLHCP should be provided information on the respirator type and weight, when and for how long it will be used at any given time, whether it is required for routine and/or emergency use, the expected physical demand/effort while wearing the respirator, additional protective clothing to be worn (e.g., firefighters suit), and temperature and humidity conditions at the workplace. The PLHCP should be given a copy of the respiratory protection program and 29 CFR 1910.134 rules for reference.
The physical efforts of the job may be estimated by preparing a physical demand analysis (PDA) for various jobs, particularly those involving wok while masked up, e.g., rig floor activities. PDAs that were developed for ergonomic assessments should suffice for this purpose.
On an offshore rig, temperature extremes, at a level that would cause heat stress, may be anticipated in work areas close to the flare, in engine, boiler and machinery rooms, and those areas receiving and processing mud returns from the well. High-humidity areas include the shale shakers and mud pit room.
Written recommendation should be sought from the PLHCP on whether the employee is medically fit to use a respirator and if there are limitations that preclude its use under the work conditions specified. The medical examination results should be discussed with the employee.
Fit Testing for Personal Protective Equipment
Each employee should be “fit tested” following medical evaluation and prior to assignment of requiring the use of a respirator. The fit test procedure should be documented in the respiratory protection program and conform to 29 CFR 1910.134, Appendix A, for “tight fitting” respirators. Fit tests are performed using a variety of facepiece sizes to select the one that fits best, and are recorded and repeated annually. The fit test is usually conducted onboard by the H2S safety officer using Bitrex or saccharin solution. H2S respirators – self-contained breathing apparatus or air line respirators – are of the “pressure demand” type; therefore, the fit test should be performed in the negative pressure mode to detect leaks.
H2S Safety Training
Training helps employees to recognize the dangers of H2S and is required to comply with 29 CFR 1910.1200 and 29 CFR 1910.120. API RP 49 recommends Action Levels of 10 ppm H2S and 2 ppm sulfur dioxide (SO2) as triggers for training. 29 CFR 1910.134 mandates initial training prior to the assumption of duties requiring the use of a respirator, followed by annual refresher training.
H2S training should address:
- Sources of H2S leaks
- Hazards of H2S exposure
- Properties and characteristics of H2S & SO2
- Proper use of detection equipment (personal or portable gas monitors)
- Recognizing & responding to alarms
- Location of muster points
- Symptoms of exposure & biological effects
- Rescue techniques & first aid
- Proper storage, use, & maintenance of the respirators
- Limitations & capabilities of the respirators
- Practical donning, operational checks, & doffing of the respirators
- Recognizing & responding to respirator malfunction and emergency situations
- Recognizing medical signs that may prevent or limit the user from wearing a respirator
The implementation of an H2S training program conforming to ANSI/ASSE Z390.1 (Accepted Practices for H2S Training Programs) is recommended.
Hydrogen Sulfide Monitoring
The objective of monitoring is to immediately identify the presence of H2S when predetermined action levels have been exceeded, so that the necessary control measures can be implemented. A fixed H2S detection system should be provided for continuous monitoring of areas where H2S is likely to be released. H2S sensors should be located in the mud logging unit, Bell Nipple/mud return trough, shale shaker, mud pit room, drill floor, and air intake to the living quarters.
The sensors should be located nearest to the point of release, at floor height (but off the floor) and protected against steam, water, mud and chemical splashes, and mechanical damage. H2S sensors work on the principle of diffusion, following Fick’s laws, and are susceptible to “poisoning” or drifting. It is therefore essential to have written requirements for periodic calibration and ensure that those are performed as scheduled.
The system should be capable of being function-tested and calibrated at the control panel, and include a power failure and fault indicator for each channel. The control panel should be located in the rig control room, which is manned continuously, and include auxiliary alarms and/or visual annunciators at the central switchboard/engine room and driller’s cabin, where controls for ventilation systems and well control equipment are located.
Personal H2S monitors should be provided to personnel that work in high-noise areas or where an area alarm might not be easily heard. Visual alarms, such as strobes, should be provided in those areas. At least two portable, direct-reading instruments should be available for personnel leading emergency response efforts, including the offshore installation manager, driller and safety officer. A calibration kit, battery charger and sampling tube/probe should be available for electronic instruments.
An adequate supply of colorimetric indicator tubes, in various detection ranges, should be available as backup for the electronic instruments. Indicator tubes are recommended when drilling wildcat wells or situations where the H2S concentration cannot be predicted with certainty. Caution should be exercised to ensure that the aspirator is compatible with the colorimetric tubes selected and that the tubes are properly stored and consumed or discarded within their useful shelf lives. Colorimetric tubes have lower accuracy and should not be used to confirm the absence of H2S.
Respiratory Protective Equipment
Respiratory protective equipment (RPE) is a type of equipment worn by workers to minimize exposure when working with hazardous substances, like gases, sprays, fumes, solvents, or dusts. RPE can usually be categorized as a respirator or breathing apparatus. Best practices dictate that RPE be designed to:
- Protect the wearer from various airborne hazards
- Suit a variety of situations
- Match the specific requirements of the wearer
Respiratory protective equipment (RPE) for H2S is selected on the assumption that all work areas outside the living quarters fall under the immediately dangerous to life and health (IDLH) definition, for the H2S concentrations that may be encountered.
The workplace and user factors to be considered in selecting RPE include:
- Time, distance, & effort required to travel while masked up from work areas to the muster/safe briefing area
- Level of physical effort required to perform the job or assist with a rescue while masked up
- Physiological & psychological state of being of the user
- Maximum use concentration
- Extenuating circumstances such as fires, spills, or structural damage to escape routes that preclude the safe use of those routes
The respiratory protection program should include:
- Written procedures for selection
- Use in routine and emergency situations
- Cleaning and disinfection
- Inspection, repairs and maintenance
- Procedures for testing the quantity, quality and flow of breathing air in airline systems and self-contained breathing apparatus (SCBA)
The RPE for H2S and SO2 on an offshore drilling rig comprises of a work/escape airline breathing air system and 30-minute SCBA units for emergency response and rescue personnel. Figure 4 illustrates a typical airline breathing air system.
The airline system comprises of a multistage breathing air compressor that charges one or more accumulators or cylinder banks (2,400 psi to 2,600 psi). The reserve or stored air capacity of the cylinder bank should be adequate to support work crews for a period of at least two hours without recharging. The high pressure from the cylinder bank is regulated down to 125 psi and distributed to low-pressure breathing air manifolds into which employees can plug at their work areas.
Manifolds are commonly located on the rig floor, within the drilling derrick (at the monkey board and stabbing board), crane operator cabs, shale shaker area, mud pit and mud pump rooms, emergency control switchboard and at the muster stations. The pressure within the facepiece is maintained at a slight positive pressure to prevent ingress of contaminated air through the seals.
The other components of the airline system include a quick-connect hose that attaches the facepiece to the manifold and a pre-charged five- to 15-minute capacity compressed air bottle for escape purposes, that is worn at the hip. The air compressors should be located at an elevated level on the rig to avoid the aspiration of H2S. This is achieved by placing the compressors at the port and starboard side of the uppermost deck of the living quarters.
One of the compressors should be engine-driven so that the system is available in the event of a power blackout on the rig during an H2S release.
The intakes for the air compressors should be routed away from the exhaust and located in a contamination-free area. High-temperature and carbon monoxide alarms (that alarm at 10 ppm) should be installed on oil-lubricated compressors, and the inline moisture trap and sorbent filters should be drained daily and replaced in accordance with a planned maintenance schedule.
Where longer hose lengths are required to permit movement, pressure-drop calculations are performed to ensure that the manufacturer-recommended pressure and flow requirements are met. Low-pressure alarms should be available for each breathing apparatus and high-pressure cylinder bank of the SAR system.
In harsh-weather environments, the rig lifeboats are commonly outfitted with airline manifolds into which occupants can plug while awaiting the signal to abandon the rig. Employees disconnect from the air manifold and breathe off their escape bottle during platform abandonment. The lifeboat air system augments this air reserve with a 10-minute supply.
Breathing air quality should be tested periodically to ensure it meets ANSI/CGA Commodity Specification for Air G-7.1-1989, Grade D, and the tests should be recorded. The specification of Grade D breathing air is:
- Oxygen content between 19.5% and 23.5%, hydrocarbon content below 5 mg per cubic meter
- Carbon monoxide below 10 ppm,
- Carbon dioxide below 1,000 ppm
- Moisture content below dew point of -50˚F at 1 atm pressure
- A lack of noticeable odor
When the respiratory protection program (RPP) is properly implemented, the MUC for airline respirators, which have an assigned protection factor (APF) of 1,000, equates to an H2S concentration of 10,000 ppm (MUC = APF x TLV). The MUC for pressure demand self-contained breathing apparatus (10-minute escape pack or 30-minute unit) is 10 times as much, i.e., 100,000 ppm, because the APF for SCBA is 10,000. Adjustments for non-standard work hours should be considered if the exposure is expected to be steady and continuous.
RPE should be stored in areas that are free of dust, sunlight, excessive moisture, chemicals and extreme temperatures. They should be packed to prevent deformation to the facepiece and other components and inspected prior to and after each use. Function tests should be performed by the user prior to taking an escape respirator into a known H2S work area.
SCBA cylinders should be inspected monthly and recharged when the pressure drops below 90%. SCBA cylinders should be tested and maintained to DOT shipping container specifications 49 CFR 173-178. 30-minute SCBAs should be provided for emergency response team members and rescuers, and those units should be labeled to identify them as such. When defects are noted, the respirator should be tagged and removed from service for repair by trained personnel, using manufacturer-recommended (NIOSH certified) parts and instructions.
Supervising a Safety Program
The RPP on offshore rigs is administered by the safety officer designated by the drilling contractor. Often, the services of an experience H2S specialist is offered as part of the package for the airline system that is leased for the duration of the well to be drilled. The program administrator should be qualified by training or experience and conduct reviews of the program effectiveness.
Other responsibilities may include:
- Assigning responsibility and frequency for RPE inspections (or performing those inspections)
- Reviewing implementation of the RPP
- Verifying that employees know how to properly use their RPE
- Scheduling repairs of RPE when needed
- Maintaining records of medical examinations, fit tests, training and inspections
- Making upgrades to the RPP when needed
Emergency Response and First Aid
Despite the numerous precautions taken to prevent H2S incidents, emergencies should be anticipated due to the extreme toxicity of H2S. A written H2S contingency plan is expected under OSHA 1910.38 and should be developed to include response procedures at the tactical level. The plan should dovetail with the company’s shore-based incident command system or plans of the operator.
Key elements of an H2S contingency plan include:
- An onboard emergency response organization
- Notification & alarm systems
- Arrangements for safe muster & personnel accounting
- Procedures for well shut-in & confining the H2S leak
- Procedures for gas-freeing affected areas & confirming they are safe for resumption of work
- Procedures for declaring the end of the emergency and standing down resources
- Search & rescue arrangements
- Training & exercising of personnel assigned emergency response duties
- First aid & medical treatment arrangements for victims overcome by H2S
- Evacuation or abandonment arrangements in the event the emergency gets out of control
It is important to plan early for H2S operations and advocates the use of engineering controls in order of priority. The article discussed administrative controls, including key elements of a respiratory protection program and hydrogen sulfide contingency plan and discussed the respiratory protection equipment that is typically selected and used in offshore hydrogen sulfide areas.
Article References:
- Agency for Toxic Substances and Disease Registry (2006). Toxicological Profile for H2S. Division of Toxicology and Environmental Medicine, US Department of Health and Human Services, Atlanta, GA.30341.
- American Conference of Governmental Industrial Hygienists, (2009). TLVs for Chemical Substances and Physical Agents and Biological Exposure Indices, ACGIH, Cincinnati, OH.
- API RP 49 (March 2007). Recommended Practice for Drilling and Well Servicing Operations Involving H2S, API Publishing Services, Washington DC 20005.
- Canadian Association of Petroleum Producers (Dec 2005). Use of International Standard NACE MR0175/ISO 15156 – Materials for Use in H2S Containing Environments in Oil and Gas Production.
- DOT 49 CFR 178, Subpart C, Shipping Container Specifications (2009).
- Occupational Safety and Health Administration.
- 29 CFR 1910.38 Employee Emergency Action Plans and Fire Prevention Plans.
- 29 CFR 1910.120 Hazardous Waste Operations and Emergency Response Standard.
- 29 CFR 1910.134 Respiratory Protection Standard.
- 29 CFR 1910.1000 Air Contaminants.
- 29 CFR 1910.1200 Hazard Communication Standard.
- UK Offshore Operators Association Limited (1985). Guidelines for Detection and Control of Hydrogen Sulphide During Offshore Drilling Operations, UKOOA, Aberdeen, UK.
- Wylie, Douglas N. and Elias, John D. (2000). Adjustment of TLVs to Accommodate Specific Conditions in the Workplace, Conference Proceedings, Industrial Accident Prevention Association, Toronto, ON, Canada.
Iam so interested to study more of the drilling safety and I request that you send me all the training modules, all drill safety modules to me on the cost please.
Thankyou,
Abel Peniel
kindly send me the drilling safety manuals and I request that you send me all the training modules, all drill safety modules to me .
Can you please advise on any regulation on the use of refuge chambers in case of an H2O release?
kindly send me the drilling safety manuals and I gratefully request that you send all the training modules including all drill safety modules to me .
Please share the drilling safety manuals and training modules.
A good and well rounded article on H2S safety. Very heartening to read and know that there are plenty of H2S safety experts around still.
H2S awareness training videos are widely available on the internet but to be certified H2S-trained would have to be done through companies.
Vega, for refuge chambers, it is dependent on the risk assessment and how secluded is the rig and also a list of various other factors.
I am interested to study moore. Kindly send me the drilling safety manuals and I request that you send me all the training modules including all drill safety modules to me .
Can you please send me the procedure how to handle if h2s contaminated rig fluid arrives at your yard area in container. dctvm1@gmail.com regards very badly required
Very interesting article, Im very interesting in the drilling safety manuals and I gratefully request that you send all the training modules including all drill safety modules.
Best Regards
Julio
This really is an interesting piece. Could you also send me the drilling safety manual and all the training modules. I believe they will be of immense help to me.
Thanks a lot!
Nick
Do you have any information regarding air supplies to temporary refuges, methods such as pressurization air from a safe area (how to define the safe area) or provisions of bottled air for pressurization.
Can you please send me the procedure how to handle if h2s contaminated waste (in supplyvessel) arrives in port.
Dennis,
If you’re receiving circulated fluid at your yard it should be screened for H2S before receiveing it. Sometime these fluids are pulled from the well pacakaged and delivered to you. Please have them screened before you accept them. If you’re not set up to screen have it done with an outside lab.
it is really informative and intrested topic discussed please send me drilling manual if possible.
very important information, please how can I have a study guide about H2S gas/ or training material
Thanks so much
I am interested to study more. Kindly send me the drilling safety manuals and I request that you send me all the training modules including all drill safety modules to me.
Thanks,
A.Kader