Holistic approach to ROP balances speed with tool reliability, hole quality
Drilling contractors deploying technologies that prioritize mitigation of downhole dysfunctions and ability to stay in hole for longer
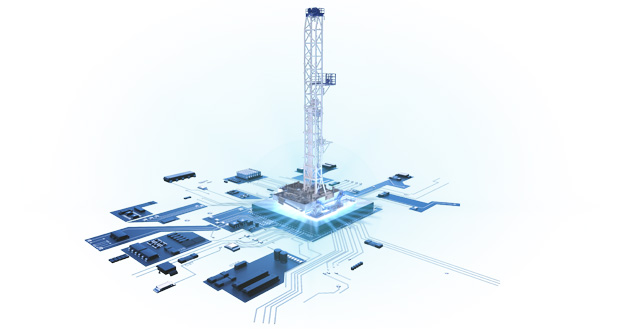
By Stephen Whitfield, Senior Editor
Conventional wisdom would indicate that optimizing well construction requires faster drilling with a higher rate of penetration (ROP). High ROPs usually indicate fast and cost-efficient operations, which should logically result in time and money savings for the operator.
However, pushing for high ROP can create new challenges when it is done too aggressively. For example, faster speeds may require the driller to run their downhole tools harder, increasing the risk for tool failure or perhaps increase bit wear. Or, a more aggressive bottomhole assembly (BHA) may need to be run, which can help reduce slide time but sacrifice wellbore quality. Other potential consequences like wellbore instability and stuck pipe can also occur. Additionally, chasing record wells can increase the possibility of catastrophic scenarios – and just one such occurrence would significantly impact any project’s economics.
With the recognition that faster isn’t always better, operators and drillers are doing more to identify and maintain the optimal ROP throughout the entire drilling process, with the goal of staying in hole for as long as possible.
“Our customers want to address well cycle time,” said Sonny Auld, Principal Product Manager at Helmerich & Payne (H&P). “They want to be able to predict how many wells they can drill in a month or a year with a given rig, but that has very little to do with instantaneous ROP, or how fast you drilled a given foot. It’s about how many feet we can drill for them in a year.”
ROP optimization requires careful attention to both dynamic and static drilling parameters. Dynamic parameters, like weight on bit (WOB) and rotary speed (RPM), can be altered quickly while drilling, and drilling contractors are deploying increasingly sophisticated automated systems that can adjust these parameters in real time based on changing downhole conditions. Although static drilling parameters, like the bit and cutter selection, can’t be as readily adjusted, they are equally important. It is only through finding the right combination of systems that consistency can be improved and long-term value can be provided, rather than pushing for one-off record ROPs.
“The challenge is to find the limiters that are holding us back from efficiently drilling at high ROP, and that requires us to look at stuff like wellbore tortuosity, geosteering, hole cleaning and making sure that we’re able to bring those up to meet the speed,” said Tino Haddad, Operations Manager at Nabors Industries. “The same way that bit providers are coming up with new cutters and motor providers are coming out with new tools to help companies drill faster, our goal is to bring everything else up to maintain that high performance.”
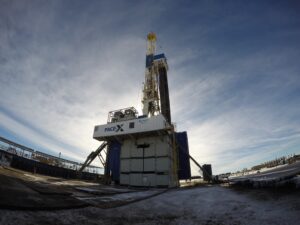
Using automation to drive efficiency
Nabors’ recent efforts in optimizing ROP center around its collaboration with Corva, which began last February. The partnership aims to employ Corva’s Predictive Drilling, a system based on AI and machine learning (ML), to help optimize ROP while reducing downhole dysfunctions. The technology was installed within Nabors’ universal rig controls and automation platforms – SmartROS and RigCLOUD – and it enables remote control of various rig site auto driller set points through a cloud-to-cloud connection.
Corva had been developing and field-testing various AI systems to optimize rotary drilling performance for around five years prior to the launch of its collaboration with Nabors. However, being able to integrate with the drilling contractor’s rig controls and automation platforms allowed Corva to take its own systems a step further by providing real-time, closed-loop control of the auto driller.
Predictive Drilling uses a rotary drilling optimized ML model to analyze drilling parameters in real time and recommend optimal set points considering minimum and maximum thresholds. The resulting setpoints are executed automatically via the integration with SmartROS, allowing for continuous control and optimization without requiring thousands of manual changes by the driller.
By being installed within the SmartROS platform, Predictive Drilling extends rig control and real-time data pipelines from the wellsite to the back office of Nabors’ E&P customers, increasing efficiency in drilling without disrupting existing workflows.
“The Corva system provides customizability in terms of what your targets are,” Mr Haddad said. “You can measure maximum ROP against things like MSE (mechanical specific energy) or directional tendency – whatever parameters you think you need to find the optimal ROP. The goal is to maximize your downhole speed while avoiding bit trips.”
Nabors first deployed Predictive Drilling on a rig in the Delaware Basin in April 2023 and has since rolled the system out to approximately 15% of its rig fleet. By the end of 2024, the company hopes to expand deployment to up to one-third of its fleet.
Results in ROP optimization have been positive so far. In one deployment on a rig in the Williston Basin in North Dakota from September to December 2023, the operator was seeking to optimize WOB, RPM and differential pressure set points within a user-defined ROP objective for six wells. By using Predictive Drilling through the SmartROS platform, the operator safely accelerated ROP while extending bit life for the six wells. This resulted in a 61% improvement in average ROP and 36 hours saved in total rig time, compared with the previous six wells drilled on the same pad.
In another deployment on a Nabors rig in the Delaware Basin in October 2023, an operator drilled lateral sections on four wells with a rotary steerable system (RSS), the Predictive Drilling system and Nabors SmartROS. There were no unplanned trips in the four laterals even while there was a 36% increase in on-bottom ROP compared with the offsets for each well, which had not been drilled with Predictive Drilling.
Outside of the Corva collaboration, Nabors also continues to deploy its REVit Z-Torque software system to improve ROP while maintaining consistency downhole. The technology automatically adjusts drilling parameters to minimize stick-slip and bit whirl, which can negatively impact performance through broken or damaged tools, decreased ROP and overtorqued connections. These issues can increase drilling time and costs.
By mitigating these dysfunctions, the system expands the efficient drilling window, allowing the BHA to stay in hole for longer periods of time.
“At a high RPM and low WOB, you’re seeing whirl and lateral vibration. At a low RPM and high WOB, you’re seeing stick-slip. Somewhere in the middle, you’ve got this pocket of stable drilling,” Mr Haddad said. “The goal of REVit is to expand that pocket by making the high frequency RPM adjustments you need to mitigate stick-slip. You’ve got a wide range of parameters to keep that window open, and through the AI modeling we use in Predictive Drilling, we can maximize use of the window.”
The system was launched in 2016 and is available not only to Nabors’ rigs but also other drilling contractors’ rigs. At the 2024 IADC/SPE International Drilling Conference in Galveston, Texas, early results were shared from the technology’s deployment in East Texas on an Independence Contract Drilling (ICD) rig from October to December 2023.
The rig was already operating with Nabors’ RigCLOUD network, which detected an unplanned trip out of hole in the intermediate section of a well. The system showed that, from 7,600 ft to 8,600 ft, the well saw an increase in stick-slip and a corresponding decrease in ROP. For the next well on the pad, REVit Z-Torque was added to the rig’s operating system, leading to a 62% reduction in stick-slip. This well also saw a 9% increase in average ROP and a 42% reduction in total days drilled. The operator also set a record for the fastest intermediate spud to total depth.
Creating a comprehensive solution
While H&P prioritizes achieving optimal ROP over the highest ROP, the company finds that it typically still sees increases in ROP speeds just by focusing on greater consistency and smoother wellbore delivery. Its latest offering, FlexFusion, allows existing control technologies to work together to mitigate the effects of bit bounce, bit whirl and stick-slip, thus improving ROP and extending BHA life. It is essentially a platform that streamlines how users can access various H&P technologies.
These technologies include Autodriller Pro, which reduces the effects of bit bounce by prioritizing stable block velocity. It is designed to smoothly control block velocity while regulating inputs from differential pressure, torque and WOB. The technology transfers to and from WOB and differential pressure while helping to maintain smooth drilling and does not require changing gain settings at the driller’s console.
The FlexTorque technology is another tool under the FlexFusion umbrella. “This technology is really about addressing the torsional vibrations,” Mr Auld said. “We want to eliminate as much stick-slip as possible. We’re trying to do our best with interpreting surface responses that may indicate a possible stick-slip, and then we’re going to do something about it. Any time you’re reducing the torsional vibrations, you are also increasing the bit life, so now you’re going from just drilling fast to drilling fast with consistent weight on bit and reduced torsional vibrations.”
A sequenced automation technology helps manage the effects of bit whirl by consistently executing the process of applying and removing WOB, he explained. “Ideally, you’re getting your maximum WOB as fast as possible, and you want to do it as fast as possible because, if you spend too much time with a low WOB, you’re getting a low depth of cut, which leads to bit whirl. We’re not going to eliminate vibrations, but we can do our best to minimize it. As we’re minimizing it, we’re increasing bit life and lateral footage per day.”
Also within the FlexFusion system is the StallAssist technology, which monitors the differential pressure based on the performance limits entered and the rate of exchange in differential pressure to detect and, subsequently, mitigate and recover from motor stalls.
Parameters can be configured within each system in FlexFusion to automatically execute pre-planned procedures for bit engagement and disengagement, slide setup and stall recovery. Mr Auld said the technologies create a roadmap that allow for greater consistency in executing procedures, which in turn enables a consistent wellbore that is less prone to dysfunction.
“We definitely believe that, if you have a consistent process and active controls working, you’re in a much better position to analyze how hard you can push the system,” he said. “This is one of the benefits of having automation – it helps you to consistently execute, and it’s easy to run analyses when the results aren’t meeting expectations. With a non-automated process, if you have 10 rigs and 40 drillers working, it’s much harder to analyze each driller’s individual processes or how they can improve well delivery times.”
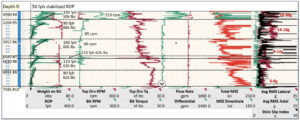
Identifying ROP limiters in geothermal
The industry is still working to overcome multiple technical and economic challenges related to scaling up geothermal drilling. One such hurdle is the extraordinarily hard rock often found in geothermal formations, which can damage downhole tools and lead to low ROP.
Over the past four years, the US Department of Energy (DOE) has funded an effort at Texas A&M University to take physics-based design workflows, originally developed for oil and gas drilling, and adapt them for geothermal drilling. The goal is to mitigate the limiters that lead to downhole dysfunctions.
The work has primarily taken place at Utah FORGE, a demonstration project that’s also funded by the DOE, aimed at developing and testing advanced geothermal systems.
The team at FORGE noted the issues they saw in applying the physics-based workflows to the first three wells drilled as part of the project – such as significant declines in ROP, especially in the early footage of each well – and then applied the lessons learned from those wells to the design of the fourth well to mitigate that ROP drop.
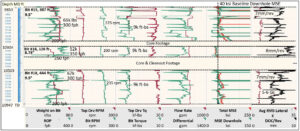
Early ROP in the first three wells averaged 250 ft/hr but then always dropped to between 70 and 95 ft/hr. The fourth well, FORGE 16B (78)-32, was drilled in 2022.
“Dropping from 250 to 95 is a huge drop in performance,” said Fred Dupriest, Professor of Engineering Practices at Texas A&M and a primary developer of the physics-based workflows during his previous career with ExxonMobil. Mr Dupriest gave an overview of his work with the FORGE team during the 2024 IADC/SPE International Drilling Conference. “If the given weight on bit is giving you a certain indentation in the first foot of the hole, the ROP should remain steady until those flats show more and more wear. So, we knew something was physically happening. Something was changing that allowed this ROP drop to happen.”
Based on results from the earlier wells, the team estimated that a stabilized ROP of 200 ft/hr should be achievable in most footage if the cause of the drop could be eliminated.
The team hypothesized six potential root causes for the drop:
- Reduced motor performance downhole;
- Traditional dysfunctions such as whirl and interfacial severity;
- Borehole patterns that might be creating loss of weight transfer in the early part of the run;
- Strengthening of granular cuttings by mechanical loading under the small wear flat observed on chamfers;
- High-amplitude, high-frequency torsional oscillations (HFTO) affecting cutter efficiency; and
- The small amount of wear observed on the edge of the cutter chamfers having a disproportionate effect on depth of cutter indentation.
The drilling motors were inspected for wear, with the team looking for a bottom-up wear trend often seen in higher temperature oil and gas wells that can lead to reduced motor performance. Not only did the motors not wear in the FORGE 16B (78)-32 well, but only two motors were needed to complete the six motor-drilled sections. Mr Dupriest said this was primarily due to the use of mud coolers, which maintained bottomhole circulating temperatures below 300°F, even as the formation temperature reached 425°F.
The limiter redesign workflow from previous wells in the project had either eliminated or mitigated traditional dysfunctions. Mr Dupriest noted high lateral vibrations in all the FORGE wells, but they were not uniquely different in the early footage compared with the later footage. They also did not record any instance of stick-slip, and bit forensics did not indicate damage from formation interfacial severity.
The team also looked at borehole image logs to determine if the loss of weight transfer was the root cause behind the ROP drop. However, even though they saw significant micro-doglegs and ledges associated with the use of a bent motor in earlier wells, there were no continuous spirals or other interference patterns that would have created a loss of weight transfer early in the run. The granular cuttings hypothesis was also disproven – strengthening of the granular cuttings would have resulted in an elevated MSE compared with the confined rock strength, and the baseline MSE for the previous wells remained close to the confined rock strength in each run.
The team observed HFTOs early in each run of the previous well, and the rate of HFTO declined with the drop in ROP, suggesting a causal relationship. They hypothesized that a form of velocity weakening and strengthening might be occurring within the bit’s rapid oscillation, which could then accelerate the creation of the small wear flat on the chamfer. Mr Dupriest said that, if HFTOs contributed to the rate of wear and could be prevented, the small flat could be delayed and higher ROP could be maintained for a greater distance.
To test whether HFTO was contributing to the early wear, an HFTO suppression sub was used in the motor-driven RSS, and a high-frequency data sub was located below the motor. If the HFTOs were successfully suppressed, and if they had been contributing to the drill rate, not only would HFTOs show as being reduced, but the ROP would also not decline as rapidly. However, the lateral vibrations were high with the motor-driven RSS, and the high-frequency data was inconclusive.
This left one other possible cause: the wear observed on the edge of the cutter chamfers. The FORGE team saw a relationship between wear and ROP in the previous well. At the Drilling Conference, Mr Dupriest highlighted representative cutters from three bits at different stages of wear on the well, and the percentage loss of ROP observed at the time the bit was pulled. The first bit was pulled after 65 ft of drilling, and there was almost no detectable wear on the chamfer edge and no loss of ROP.
The second bit, which was pulled at 341 ft, showed wear flats across 30% of the diamond table and a 65% loss of ROP from the start of the run. The third bit, pulled at 688 ft, showed wear flats across 50% of the diamond table and a 70% loss in ROP.
Previous testing at FORGE indicated that increased depth of cut from higher WOB reduced the wear per foot, not only increasing ROP but also enabling the bit to drill more footage. For the FORGE 16B (78)-32 well, the team opted to use a 9½-in. bit as opposed to the 10¾-in. bit it had used on the previous wells, increasing the load per area. It also opted to increase the depth at which the cutters travel, increasing the aggressiveness of the bit’s cutting structure.
The ROP decline trends for the first five 9½-in. bit runs on FORGE 16B (78)-32 showed an aggressiveness similar to previous wells. The first was run with a motor-driven RSS, so the initial ROP was high. However, the ROP decline trend was the same. The initial ROP of the remaining four bits was lower due to reduction in bit speed from 210 rpm to 60 rpm as the motor was laid down because of high vibrations in the motor-driven RSS. The slope of the early decline trend was still the same with the lower RPM, and the stabilized ROP of all bits was around 50 ft/hr.
The team then decided to run bits with more aggressive cutting structures, using eight-bladed bits as opposed to the six-bladed bits used in the previous five runs. The initial ROP was 300-350 ft/hr, but more importantly, the stabilized ROP remained higher, leveling out between 200-250 ft/hr.
Mr Dupriest said the depth of cut shown in the last three runs may be of interest in designing bits for future geothermal wells. The bits advanced at 7-8 mm with each revolution (0.27-0.31 in.). Many bits used in both geothermal and oil and gas are designed with backup cutters set at a height to engage before the primary cutters are indented to this depth. With ROP approaching 300-350 ft/hr, Mr Dupriest said operators will need to work with bit vendors to ensure ROP is not being limited by the backup cutters or rubbing surfaces as step tests are run to test performance at higher WOB. The offset in backup cutters should be documented along with other bit features, such as blade count. DC
Click here to watch DC’s interview with Fred Dupriest on the challenges of the FORGE project.