Technology advances see offshore drilling firmly move to the digital realm
Industry pursues increased efficiencies through real-time KPI tracking, fuel consumption monitoring and a rig-specific digital twin
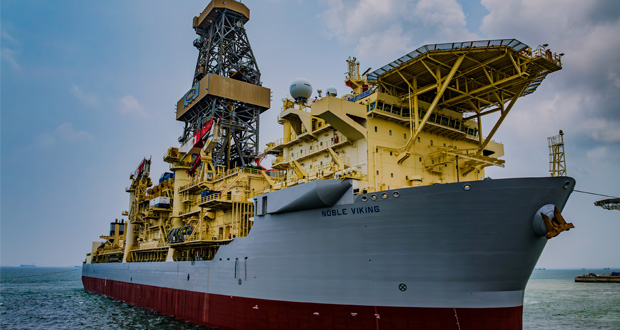
By Stephen Whitfield, Senior Editor
The offshore drilling space has seen a multitude of technological innovations in the past decade, with systems aimed at improving not only the rig’s performance but also crew safety, as well as reducing the carbon footprint. “We have far fewer floaters running now than we did before, and we’ve done what we can to make the rigs efficient,” said Thiago Schimmelpfennig, Chief Commercial and Innovation Officer at Constellation. “All the lower-hanging fruits in terms of upgrades and changes to the engines, we’ve mostly performed that. So, innovation is going to be critical to fine tuning what we can do with our fleet.”
Constellation and Petrobras, for example, are collaborating on a rig-specific digital twin technology that will streamline the identification of energy-saving upgrades and technologies. Noble recently finished rolling out its own technology focused on providing its teams with precise, rig-specific data so they can analyze for ways to achieve more energy-efficient operations. Embedding the use of data into operations, and using that data in a range of existing processes and workflows, will enable Noble to make energy efficiency an integrated part of the way it runs its rigs.
“Using data in the right ways allows us to have better conversations internally to change behaviors on our rigs,” said Freddy Reyes Falck, Senior Director of Innovation and Sustainability at Noble. “It allows us to have better conversations with our customers and show them, for example, what trends in consumption we might see if we install a variable frequency freshwater pump. We can show the potential improvements, and the customers can see the value. That makes them more willing to co-invest with us in improving and upgrading our rigs.”
Kongsberg Digital is also working on a solution that can help drillers and operators optimize their drilling and well operations by analyzing sensor data in real time. Evaluating that data with intuitive software applications leads to better understanding of rig operations in real time.
“Our business is about finding insights from operational data,” said Edward Streeter, VP – Wells at Kongsberg Digital. “The easiest thing to do is to look at sensor data on a screen, but think about all the learnings we’ve captured in the past. How do we leverage those insights? By integrating and contextualizing the data that allow us to turn that raw data into something that has more actional value. Our end users are drowning in data, and we have to help them.”
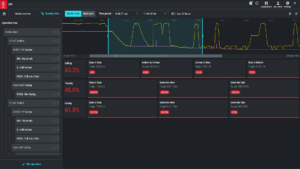
Tracking performance indicators
In late 2022, Kongsberg Digital launched an application that allows drillers and operators to follow key performance indicators (KPIs) on drilling and well operations – like slips to slips and flat times during BHA makeup – in real time.
“If you’re an operations manager or a toolpusher, you want to understand if you’re meeting your targets,” Mr Streeter said. “You want to know whether there’s some sort of trend happening with a particular rig crew. Are people getting fatigued as you come closer to crew change? Was there a mechanical breakdown or some issue with your rig that really affected your statistics? What we’re doing is putting things at the fingertips of the end users, so they don’t have to spend hours finding information. You have this system running automatically without the need for a human to curate everything into a report.”
The app is a “workflow targeting a specific set of users for a particular problem,” he explained. Proprietary algorithms are used to allow for real-time data and conditions-based logic to be integrated, analyzed and applied to track the KPIs, so that users can immediately identify potential areas for boosting efficiencies on the rig.
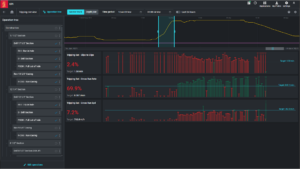
“You don’t have to wait until the daily drilling report comes out,” he said. “You can literally follow what happened in the last couple of hours in your well. If your performance is inconsistent or unexpected, you can see that. But the interpretation is self-explanatory to the end users. We’re giving you the information, and then you can figure out why, for instance, you’re being inconsistent? Are you having trouble with something?”
While the application was launched with just four drilling KPIs – slips to slips, slips to bottom, bottom to slips and bottom to bottom – Kongsberg Digital has since expanded the offering to encompass 46 KPIs. These include a KPI measuring connection times – where relevant, the system splits the results based on direction to include run in hole and pull out of hole.
In addition to the drilling KPIs, the app now also measures slips to slips, gross running rate and gross running speed during tripping, casing and riser running. It also captures flat times during BHA makeup, BHA break-out and BOP testing.
“Our goal since we released this app has been to keep improving it,” Mr Streeter said. “We want to improve the user experience, the filtering of data and add more KPIs. Our goal is not to offer too many KPIs. It’s about focusing on what are the key ones that users want.”
The application is part of Kongsberg Digital’s SiteCom platform. Launched in 2003, SiteCom is a WITSML-compliant system that collects data from multiple sources, including the rig control system, the mud loggers, or the measurement-while-drilling systems. That data then becomes available on internal and third-party applications integrated within the platform.
Along with the KPI application, SiteCom hosts native apps for monitoring ongoing well operations, collaboration between remote stakeholders and the capture of lessons learned.
Improving granularity in monitoring power usage
In 2023, Noble completed the rollout of a new fuel consumption monitoring system across all 29 rigs in its fleet to support energy-efficient operations. The system, Energy Efficiency Insights (EEI), is a software program that tracks, analyzes and models CO2 and NOx emissions data, thereby allowing its engineers to gain insights into potential emission reductions.
Through sensors that have been installed around the rig – like flowmeters connected to the rig’s engines that measure fuel consumption, or other sensors connected to key energy-consuming equipment on the rig, such as the drawworks, top drive, mud pumps, lighting systems and air conditioning systems – the EEI system collects measurements on the amount of power being used in real time.
Those sensor data are automatically directed to Noble’s onshore cloud computing database via servers located on the rig. The EEI software accesses the data from this database, and then models how power is consumed on the rig.
“The idea behind this was that you can’t change the things you can’t measure,” Mr Falck said. “There was a realization that we needed to measure exactly how much energy and fuel each individual component was burning, and that can give us a baseline to determine what we may need to address in order to reduce our emissions.”
Users can access the data via an application that’s available on desktops, laptops and mobile devices. The interface displays all of Noble’s active rigs on a map, along with the name of the operator for which each rig is running. For any given rig, users can see its daily fuel usage, which can then be broken down into smaller or larger units of time – like an hour or a month.
Additional tabs in the app show the average fuel usage per day on the rig, total CO2 emissions, total NOx emissions and the average CO2 and NOx emissions per day. Users can also view the power usage for the main subsystems on the rig, with a corresponding calculation of fuel usage and corresponding emissions for that subsystem.
The EEI software helps enable the optimization of daily activities and an understanding of the impact various energy efficiency initiatives can have on greenhouse gas emissions.
Mr Falck said that the multitude of new sensors added to each rig means that fuel consumption and the associated emissions from equipment power usage can be monitored and tracked back to specific energy consumers and types of operations. This can provide the basis for further modeling and identification of best practices for using equipment on the rig, encouraging sustainable fuel consumption.
Prior to adopting EEI, Noble had a fuel-monitoring database that incorporated data requiring manual input by rig personnel, who would examine the fuel levels for each tank on 12-hr shifts. While that system provided a rough baseline of fuel consumption, it was prone to human error – “if one of operators makes a typo, all the data is screwed up,” Mr Falck said. Further, that approach was limited in scope, as fuel consumption from the engines did not provide a comprehensive blueprint for improving energy efficiency. Placing sensors on the rig’s equipment and connecting the power usage to fuel consumption in a single interface, he said, provides a more granular picture of how the rig’s equipment affects its overall energy consumption.
“If we make a change on the rig, like replacing a freshwater pump, we can compare the trends. Did that replacement actually have an effect on power usage and fuel consumption? If so, what effect did it have? It’s basically validating and understanding how our behaviors and our upgrades affect that energy consumption,” Mr Falck said.
Upgrades on the Noble Invincible jackup, for instance, included a battery energy storage system and the EEI monitoring software. The battery system enabled storage of excess power from the drawworks, which made it possible to level off power peaks to obtain a constant load on the main engines, reducing fuel consumption. The EEI software then allowed Noble to track fuel consumption on the rig. By multiplying that fuel consumption against a carbon emissions factor, an estimate of the carbon emissions intensity from the rig can be calculated. The battery system has led to a 21.5% reduction in carbon emission intensity since its implementation through the end of last year.
“We’ve been able to easily visualize the improvements achieved from this hybrid system on the Noble Invincible,” Mr Falck said. “It’s an instance of being able to validate and show the proof that what we’re doing and what the customer is investing in, is generating a return.”
In 2024, Noble added a new operations functionality to the EEI system, with the aim to make the data more actionable. The functionality allows users to break down power usage for various pieces of equipment by the type of activity that is occurring. For example, energy consumption can be broken down into drilling versus tripping or running casing.
“Energy consumption is different during drilling versus during running casing. So you might see the consumption of a piece of equipment go down one week and up the next week, but it’s solely because of the operation. Comparing energy consumption without the operation is comparing apples to oranges. When we look at the consumption per hour for a particular operation, it then becomes an apples-to-apples comparison,” Mr Falck said.
By the end of this year, Noble anticipates adding another tab within the EEI system that visualizes energy consumption during bad weather events. “Weather really plays a major role in the energy consumption you’re going to see on any drillship. If we can find a way to normalize the data we see from various wind and weather events, that will give us a better indicator of our trends.”
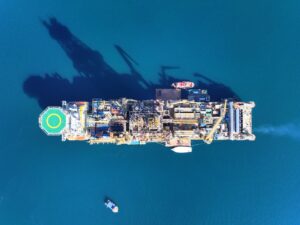
Using digital twins to test upgrades
Late last year, Petrobras and Constellation began a project with the University of São Paulo to build a digital twin modeled after Constellation’s Brava Star, an ultra-deepwater, dynamically positioned drillship working offshore Brazil. The digital twin will allow the companies to test potential equipment upgrades on that rig and other similar Constellation drillships running for Petrobras, with the primary goal of identifying technologies that can increase energy efficiency on the rigs.
This marks Constellation’s first digital twin project. And while Petrobras has undertaken several digital twin projects before – most recently, it announced a partnership with Halliburton on the Mero field at the end of last year – previous projects had modeled wells, reservoirs and production facilities. Modeling a drilling rig specifically will be new, although Mr Schimmelpfennig said Petrobras’ experience with digital twins will be a valuable asset.
“Petrobras has all of the operational knowledge about the wells, and Constellation will provide all the details on how our rig works – the subsystems, the operational sequences, and the integration of different data from the rig. The team at São Paolo will then bring all the information together into one model. I think the combination of all of that will make this an effective collaboration,” he said.
José Ricardo Brígido, Research, Development and Innovation Engineer at Petrobras, said that the partnership with Constellation primarily spawned out of the operator’s interest in taking a comprehensive approach to energy efficiency.
Even though it does not own the rigs, working with a drilling contractor on such a project will provide insight into the types of technologies the operator wants to see implemented across its contracted rig fleet.
“We realized that we can’t determine if the possible technologies we’re looking to put on a rig are more or less effective if we don’t know the exact meteorological situations, the operational demands and the risks of the operations in real time. The wells we drill are often in complex environments, so how can we visualize this operational and well risk more effectively? The digital twin is going to be a fundamental rock on which we answer those questions,” Mr Brígido said.
The companies aim to have a completed twin of the Brava Star by mid-2025. The drillship was selected for this project because it is one of the newest and most modern drillships in Constellation’s fleet. It currently has flowmeters running on the engines, as well as sensors on the dynamic positioning system and on key equipment such as the top drive.
These sensors were previously put in place by Constellation to monitor power consumption from the rig in real time, but Mr Schimmelpfennig said they are serving as key starting points for building a full model of the system. “Brava Star is our most well-equipped rig in terms of monitoring and sensors. It is already able to provide a lot of inputs for us, so in building the digital twin we can know exactly what inputs, what variables we’re able to monitor, without having to install an expensive monitoring package on another rig.”
The digital twin will help Constellation and Petrobras analyze the potential for several decarbonization initiatives the companies are evaluating for the near future. For instance, the companies want to explore the viability of installing energy storage systems on Constellation’s drillships, including battery energy storage systems and flywheel energy storage systems.
“For all of these initiatives, you need an enabler, and this project we’re doing with the digital twin is going to be the enabler,” Mr Schimmelpfennig said. “We can evaluate these technologies without necessarily testing them offshore in very complicated and complex operations. We intent to simulate these initiatives within the digital twin to really understand what our targets should be, and to give us an idea of what impacts these initiatives would have on consumption.” DC