Drill bit innovations target major barriers to ROP, durability
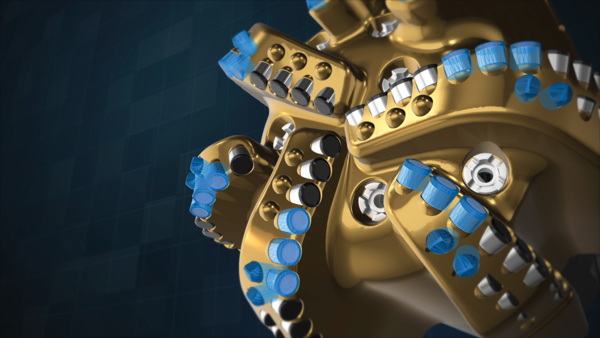
Manufacturers are developing new bits that address cuttings evacuation, vibration and thermal degradation while rearranging cutter layouts and seeking better understanding of failure mechanisms
By Kelli Ainsworth Robinson, Associate Editor
- Drill bit providers are further optimizing hydraulics to improve cuttings evacuation.
- New blade designs and cutter geometries are being used to reduce vibration, impact and heat damage to the bit and BHA.
- Improved manufacturing methods and higher computing power are also significant enablers for advanced bit innovations.
Although a drill bit is but one component of a large and complex drilling system, it can have an outsized impact on the efficiency of a drilling operation. “While the amount of money spent on drill bits may be less than 1% of the total cost of the well, it can really be argued that no single component contributes more to the overall drilling performance,” said Wiley Long, Bits and Drilling Tools Product Champion at Smith Bits, a Schlumberger company.

In response to these needs from operators, service and tool companies have used advanced modeling and finite element analyses to understand the major barriers to ROP and durability, including poor cuttings evacuation, high thermal generation and vibrations. Based on these understandings, they’ve developed new cutter geometries and layouts and improved the hydraulics of the bit.
Whenever possible, operators want to drill an entire section with just one drill bit, said John Campbell, Global Business Development Manager at Halliburton. “Operators want to see bits that can effectively drill straight ahead in the vertical sections and can deliver high doglegs and good directional control with high ROP in the laterals,” he said. “Naturally, they also want to achieve this with one bit run, shoe to shoe, as often as possible.”
For a bit to drill for so long, especially in laterals that exceed 10,000 ft, it must be rugged and durable. Further, as contractors build rigs with higher-powered pumps and directional companies roll out high-powered motors, a lot more energy is being delivered to the bit, Mr Campbell noted. “We’re seeing that we need more material strength and more durable bits just to handle the power that’s getting to these bits.”
In the past, increasing ROP often would decrease durability. But in today’s drill bits, higher bit durability and ROP can go hand-in-hand, Mr Campbell said. “Historically, with drill bits, you had to balance these competing objectives,” he said. “When we tried to increase the durability of the bit, often through increased diamond volume, that would hurt the ROP.” Now, advances with cutter layout in drill bits have helped eliminate this either/or proposition, he added. Cutters are remaining sharper for longer, helping operators to maintain ROPs throughout the section being drilled.
Rethinking hydraulics
The faster a bit drills, the more cuttings it produces in a given period of time. If those cuttings build up, it can reduce ROP and sap drilling energy. Additionally, cuttings buildup can insulate and create friction at the bit, resulting in higher temperatures around the bits and cutters. It’s not uncommon for stagnant cuttings to cause a rise in temperatures at the bit, which can cause degradation of the diamond and damage the cutter, said Chris Casad, Innovation Project Manager for Ulterra. “Having lower temperatures reduces damage, which means you have sharper cutters for longer, and that keeps you drilling at a high level for the entire duration of your well.”
After multiple years of development and testing, Ulterra will release SplitBlade, a PDC bit with optimized nozzle placement and fluid channeling, in late March. The placement of the nozzles and channels, which was determined through the use of computational fluid dynamics (CFD), improves the evacuation of the cuttings.
Additionally, the cutters on the bit’s inner blades are advanced forward, engaging the formation earlier and enabling better toolface control, Mr Casad said. This improves the blades’ grip on the formation, enabling better directional control.
Bits designed with SplitBlade technology have two dedicated channels of evacuation for each primary blade, as well as nozzles at the cone and shoulder of the bit. This allows SplitBlade to “separate the cutting evacuation from the cone of the bit and from the shoulder of the bit,” which are the two areas most prone to cuttings accumulation, Mr Casad said. Keeping the cone clean enables better directional control and steering, and keeping the shoulder clean allows the bit to drill faster.
Typically, when cuttings are evacuated from the bit, cuttings from the cone pass by the shoulder and can build up in that spot. With this new bit technology, the dedicated nozzles and channels at the cone and shoulder give the cuttings a more direct path away from the bit. “In addition, the shoulder isn’t burdened by all those cone cuttings anymore and is freed up from having to deal with that volume of rock. It can put its energy into drilling faster,” Mr Casad elaborated.
The placement of the channels and nozzles, along with nozzle orientation, was determined through CFD and was conceptualized with hydraulic optimization in mind, Mr Casad said.
Ulterra performed computer simulations with different jet and nozzle sizes, nozzle placements and nozzle orientations to determine the optimum flow path for cuttings evacuation and the best design to achieve that flow path. “We used the CFD simulations to dial in and hone the right place to put those nozzles, the right way to orientate the nozzles to work together with the cutting structure and with the blade structure.”
The use of the CFD simulations also led to the recognition that the nozzles on a bit’s primary blades are often oriented in such a way that the flow paths from each nozzle get in the way of one another. “The outer nozzle actually works to seal off the inner nozzle’s flow and to prevent it from exiting the bit,” Mr Casad said. Ulterra then ran additional CFD simulations to determine the nozzle offset and orientation that would create separate and uninterrupted flow paths for each nozzle.
SplitBlade bits have drilled nearly 3 million ft to date and have been used on more than 300 rigs, according to Ulterra. It was first deployed in a field test in Lavaca County, Texas, in the Eagle Ford, last summer. Operators using the bit have seen an average 30% ROP gain compared with offset data, Mr Casad said. In one Lavaca County well, the bit drilled the curve and lateral sections – totaling more than 11,000 ft – in 68 hours, for an ROP of 172 ft/hr. The dull condition of the bit after the run was 1-1-TD, showing low wear on the cutters due to better hydraulics, thermal management and cuttings evacuation.
Since its initial deployment in Lavaca County, Ulterra has run the bit for operators in field tests all over the Eagle Ford. It’s also been used in East and West Texas.
Mitigating vibrations
Lateral, torsional and axial vibration can shorten the life of a drill bit. It can also damage the bottomhole assembly (BHA) components, including downhole motors and measurement-while-drilling (MWD) tools, Mark Freeman, Director, Technology & Global Assembly, Maintenance and Overhaul, Drill Bits for Baker Hughes, a GE company (BHGE), said. “The smoother that we’re able to drill and the less vibration that we generate, the less wear and tear we’ll have on the BHA and motor.” The company launched the Kymera Mach 4 and Dynamus bits in early 2018 and July 2017, respectively, to extend the life of both the bit and the BHA by reducing vibrations.
The Mach 4 bit is the latest iteration of the Kymera hybrid drill bit line. Kymera bits include PDC fixed cutters, as well as roller cones. The fixed cutters shear the formation but can be prone to vibration due to changes in torque that can occur in interbedded formations. “When we add those rolling elements onto the frame, it helps to smooth out the torque response as you change between different types of formations.” The Kymera bits have been shown to reduce torsional vibration by between 50% to 60%, depending on the formation, according to BHGE.
With the Mach 4 bit, the company is aiming to enhance the durability of the Kymera cutting structures in hard and abrasive formations. It has introduced sharp, conic-shaped tungsten carbide inserts to the roller cone cutting structure in place of the more blunt or rounded inserts used previously. The inserts have also been packed more tightly on the rolling cones.
“Having that sharp insert helps more effectively fracture the formation. As the cone is rotating and as the tungsten carbide inserts engage with the rock, it’s punching into the rock and cracking it open,” Mr Freeman said. Essentially, the inserts pre-fracture the formation before the PDC blades shear it away. “That also helps to keep the cutting structure sharper for longer,” he added. When the cutting structures remain sharp, it prevents the ROP from suffering due to dulled cutters.
BHGE has also given the Mach 4 bit between four to six blades, depending on the application, which is an increase over the two to three blades that previous iterations of the Kymera bit had. This increases the diamond volume on the bit “so it can drill longer intervals with less chipping or breaking of the cutters,” Mr Freeman said. A new technology called ShadowCut has also been added to the shoulder of the PDC blades. These are recessed cutters that help improve the durability of the cutting structure.
To date, the Mach 4 bit has been deployed in more than 120 runs in regions like the North Sea, Middle East, US land and the US Gulf of Mexico. In one North Sea application in Q3 2017, the bit was used to drill a 16-in. section with a 70° inclination tangent. The base of the section was highly interbedded with hard sandstone and coal stringers, which can cause high levels of vibration and limit ROP. Previously, the operator drilled this hole section with PDC bits that had conic diamond inserts and experienced significant damage, poor steerability and low ROPs.
The operator then used a 16-in. Kymera Mach 4, which drilled at 87 ft/hr (26.6 m/hr), increasing the section ROP by 40% over the PDC bit and 26% over the Kymera XTreme hybrid drill bit. The Mach 4 also drilled 14% further than the offset PDC bit, saving an estimated $105,000 for the operator. “The sharp, dense cones and the increased blade count on the PDC cutting structure resulted in a huge boost in terms of drilling efficiency,” Mr Freeman said.
Like the Kymera Mach 4 bit, the Dynamus bit was developed to extend bit life and boost ROP, particularly in hard and abrasive formations. BHGE incorporated two technologies that had been developed but not yet deployed into the Dynamus: the StayTrue diamond elements and StayCool 2.0 cutters.

The StayTrue elements are chisel-shaped and placed along the bit blade. They engage with the formation as the bit drills and creates a groove in the formation. Due to its chisel shape, the element essentially rides in the groove and helps prevent the bit from moving from side to side, increasing lateral stability. “By keeping the bit drilling in a more stable way, all that energy that you’re putting into the drill bit is actually being used to cut the rock, rather than being lost to vibration,” Mr Freeman said. He noted that in one run, when the Dynamus bits were run in the field with BHGE’s MultiSense dynamics mapping system installed at the bit to measure vibration, a 90% reduction in vibration was noted compared with a standard bit.
While traditional PDC cutters have a flat surface, the surface of the StayCool 2.0 cutters is recessed in the center, with a lip around the edge. As the rock is drilled, the cuttings are released more readily off the face of the StayCool 2.0 cutter, preventing the buildup of friction and heat. “On a standard cutter, that rock would continue to travel up the face of the cutter until it reached the top before it would lift off the face of the cutter,” he said. Keeping the temperature lower can reduce thermal degradation to the diamond in the cutters and keeps the cutters sharper for longer.
Since its launch in summer 2017, the Dynamus bit has been run in the Permian, Eagle Ford, SCOOP, STACK, Bakken, Niobrara, Marcellus, Saudi Arabia, Kuwait, Canada and Oman, as well as in the North Sea and Gulf of Mexico. The product family now accounts for 20% of BHGE’s PDC portfolio, Mr Freeman noted.
In a 2017 run in the Midland Basin, a Dynamus drill bit helped an operator improve ROP by 32%. Previously, the operator had to run multiple bits in the 12 1/4-in. vertical intermediate section because the bits were experiencing significant wear and impact damage due to interbedded formations and high-strength stringers. Additionally, the ROP was compromised because of poor directional control, which required frequent corrections. The operator’s goal was to drill the entire section with a single bit, with a sustained high ROP.
When the Dynamus was deployed, it drilled 6,194 ft (1,888 m) in a single run – further than any previous 12 1/4-in. bit the operator had used in the same section. The bit drilled at a rate of 84 ft/hr, which was 32% faster than the offset bit. Additionally, the dull condition of the Dynamus after this run was 1-1; a previous bit used on the same pad, with the same rig, had a dull condition of 3-4.
Bringing in backup
The shape and material of a cutter or insert can improve a bit’s durability and ROP, but so can the layout of the bit’s cutters, Halliburton’s Mr Campbell said. In late March, the company will introduce a new cutter layout, the Stega, which features backup cutters that radially offset the primary cutters.
Using radially offset backup cutters creates the same effect on ROP as using larger, more aggressive cutters but without the detrimental effects on durability, Mr Campbell said. “The larger cutters would attack the formation more aggressively and boost ROP. Unfortunately, these cutters had a less solid cutting structure, so it would wear down faster,” he explained. “With Stega, we can drill as fast as these aggressive bits, but we still have a very durable bit.”
Typically, a row of backup cutters is located immediately behind the cutters it’s backing up. However, this can lead to the backup cutters passively grinding rock, creating friction and heat, which can damage the bit.
In Q1 2017, a bit with the Stega layout was used to drill a 2,900-ft long, 9 1/4-in. section of a well in Kuwait. This section passes through the Zubair, a soft sandstone with intercollations of shale. From there, it runs through the Ratawi formation, which consists of shale, sandstone and limestone interbedded with shale. Finally, the section passes through the Minagish formation, which is a very hard limestone with low porosity. It’s not uncommon for operators to use two drill bits to drill this section.
“It’s difficult to design a bit that’s going to have enough durability to drill these different formations with an acceptable ROP to survive the run,” Mr Campbell said. When the Stega was deployed on a bit drilling this section, the operator was able to drill the entire section with a single bit and double the drilling footage achieved in offset runs, with an average ROP of 19.84 ft/hr. When the run was complete, the bit had a dull condition of 1-1. “We took the entire interval out in one bit, and we did not compromise the overall section ROPs, so ultimately we saved a trip plus the cost of an additional bit,” he said.
In another run in the Mulicinco formation in Argentina, a Stega-layout bit was able to double the footage per run, from an average of 1,250 ft per run to 2,395 ft per run. “The prior runs were averaging about 21.9 ft per hour, and the Stega bit came in at about 20.9 ft per hour, so it’s very similar ROP with double the footage, which was the objective of the field run,” Mr Campbell said.
In addition to Kuwait and Argentina, the Stega design has been run in the North Sea, Oman and the Rockies in the US.
The Stega design will be an optional feature for Halliburton’s GeoTech fixed-cutter PDC bits platform, launched in 2017. “GeoTech was designed to utilize our latest materials technologies, modeling technologies and cutting structure technologies, packaging them into a platform that our design and field engineers can then adapt to customize according to customer needs,” Mr Campbell said.
New configurations for better attack
Smith Bits has also been developing new cutter configurations to minimize damage and dulling during long runs. “The name of the game is keeping your cutting structure sharp for the entire interval so it’s able to drill with a higher ROP consistently throughout the entire run,” Mr Long said. In November 2017, the company launched the Xplorer Helix spiral TCI configuration, a roller cone bit with tungsten carbide inserts (TCIs) arranged in a spiral configuration. “The spiral layouts of Xplorer Helix configuration increase the amount of contact area that the inserts are making with the bottom of the hole for every bit rotation.”
When TCIs on a roller cone bit are arranged in concentric rows, as they typically are, they’re vulnerable to insert tracking, according to Mr Long. As the bit drills, it creates craters in the formation. “If you’re falling back into an existing crater, you’re not getting very efficient rock crushing,” he explained. The spiral layout eliminates this effect and ensures that every insert makes contact with fresh rock as the bit drills. Reducing insert tracking also prevents the inserts from breaking and allows the cutting structure to remain sharp.
The spiral layout of the Xplorer Helix configuration was modeled using the IDEAS integrated dynamic design and analysis platform suite of finite element analysis tools, providing insight into how various TCI layouts would crush rock. “We ran simulations and monitored how the inserts were contacting the bottom of the hole and how that translated into ROP,” Mr Long said. “Then we created initial iterations of our cutting structure.”
He noted that company had considered developing a spiral insert layout in the past, but it was only with recent advances in computing power, which allowed the company to produce more complex and realistic models, that the Xplorer Helix configuration was able to go from idea to reality.
In 2017, the Xplorer Helix configuration was deployed for Kuwait Oil Company to drill a vertical 28-in. section from 500- to 5,000-ft measured depth through an interbedded formation of soft and hard limestone, dolomite, anhydrite and shale layers. This formation had compressive strengths ranging from 6,000 to 24,000 psi. “The highly interbedded nature of the interval often caused insert breakage,” Mr Long said, and translated to reduced ROP.
When the Xplorer Helix configuration was deployed in this section, it achieved an ROP of 43.9 ft/hr, which is 107% higher than the field-best ROP of 21.1 ft/hr in similar applications. Ultimately, the operator saved four drilling days using the new bit. “We were able to eliminate the risk of insert tracking and keep the cutting structure sharp throughout the interval,” he said. “Couple that with the more efficient crushing action and we were able to more than double the ROP.”
Durable materials

It’s important to understand the factors that limit the life of a drill bit in a given formation, Tom Roberts, Director of PDC Strategy for National Oilwell Varco (NOV), said. “We’re trying to understand the failure mechanisms that we’re dealing with and then develop technologies that will reduce the chance of dulling the cutters so that we can drill much faster.” Thermal degradation and impact damage are two common modes of bit and cutter damage, so NOV designed its ION cutters to resist those two elements specifically.
The ION cutters, with a 3D geometry, were launched in mid-2017. Extensive lab testing – including thermal, abrasion, impact and toughness tests – was conducted to develop a new range of application-specific diamond grades that are less vulnerable to wear and heat damage, Mr Roberts said. The company also increased the strength of the diamonds in the ION cutters by applying more pressure to the diamond during manufacturing, making it denser and tougher.
Additionally, NOV uses a deep leaching process to selectively remove the cobalt from the diamond table. “What that means is the cutters can now take a much higher temperature when drilling through the formation,” he said. Normally, PDC bits start to break down at temperatures in excess of 700°C, he noted, but the ION cutters can tolerate temperatures up to 1,100°C.
These sorts of manufacturing improvements are enabling a revolution in cutter geometry, Mr Roberts said. “Improved technologies allow us to revisit geometries that we tried or considered in the past but wouldn’t work because the durability wasn’t there,” he said.

Among these new geometries are the ION 3D cutters, which have a pointed, rather than cylindrical, geometry. This shape creates cracks that propagate to the surface. Cylindrical cutters typically crack the subsurface, which is less efficient and generates larger cuttings. Further, “we’ve seen that for a given ROP, we would actually have a lower torque using pointed 3D cutters, which is very important to operators,” Mr Roberts said.
Minimizing torque and drag reduces wear on BHA components and avoids motor toolface fluctuation and stall for greater directional response. All of this translates to reduced wear and impact on the bit and cutters.
While the 3D cutters were originally developed with carbonate formations in mind, NOV found in lab testing that the pointed geometry worked well in every formation type to which it was applied, Mr Roberts said. The cutters have been widely deployed on bits in Alaska, Canada, the Williston Basin, the US Mid-Continent, West Texas and Oman. Overall, more than 10 million ft have been drilled using ION 3D cutters.
In early 2018, an NOV bit with ION 3D cutters was used to drill a two-mile lateral in a well in the US Mid-Continent. The bit drilled 10,028 ft in 66.31 hours, with an average ROP of 151 ft/hr. In a prior application last year in north Louisiana, an NOV bit equipped with ION cutters drilled an entire lateral section, from 11,475 ft to 17,115 ft, with a single bit. Operators had been using two and often three bits to drill that same section, Mr Roberts said. “One particular operator mentioned that they strived for 1,000 ft per day, but that didn’t often happen. We set a 24-hour record for them of 1,592 ft.”

NOV is currently field-testing an ION 4D cutter. In addition to the point-loading effect provided by the ION 3D, the 4D shape will create plowing and shearing effects to the formation. In the Williston Basin, the ION 4D was recently field-tested in a well on the same pad where the 3D version had previously been used. The 4D increased the ROP from an average of 139 ft/hr to an average of 160 ft/hr, Mr Roberts said. Field testing for the 4D cutter is expected to continue through at least the first half of this year. DC
SplitBlade is a trademark of Ulterra. Kymera Mach 4 and Dynamus are trademarks of BHGE. Stega is a trademark of Halliburton. Xplorer Helix is a mark of Schlumberger.
Is the “Drill bit innovations target major barriers to ROP, durability” article part of a theme?
The reason I ask is that I believe there would be a great follow on story to this one… specifically on drilling dysfunction generated at the bit, but dysfunction that cannot be addressed by the bit but another drilling tool further up in the BHA.
There are a number of tools that reduce vibration in some form (axial, lateral & torsional). There is Neo-Oiltools with their NeoTork, Tomax with their AST, Cougar with their MacThruster and Franks with their Hi-Tool. Some of these address only a single source of vibration while others address all three.
Food for thought…